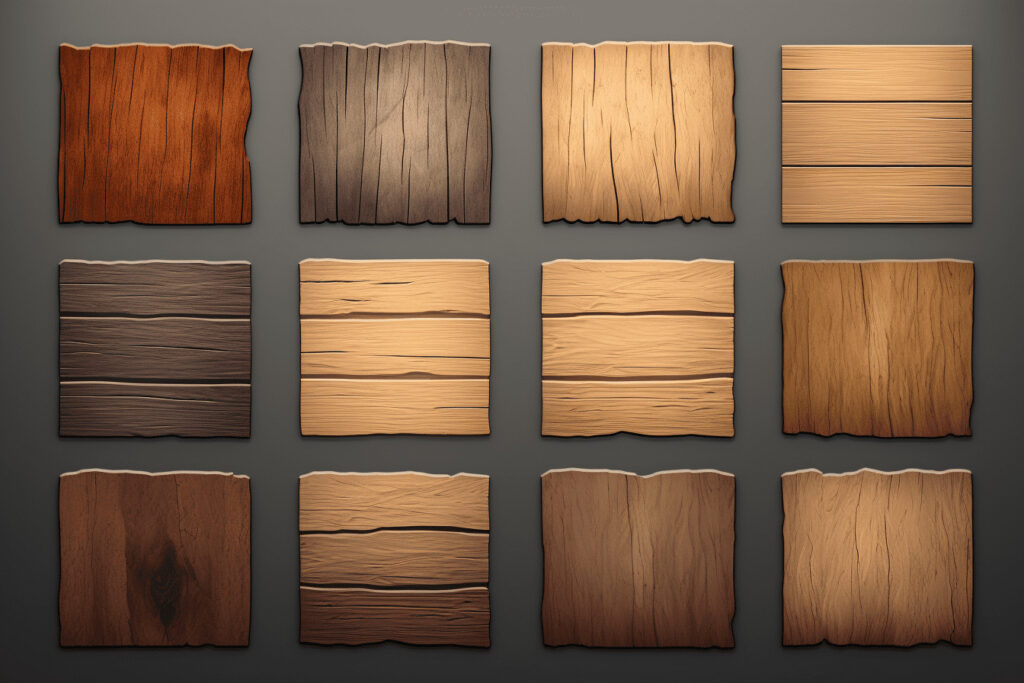
What to look for Cutting Board Wood Types
The selection of the appropriate type of wood for cutting boards must meet the fundamental requirements that I have already outlined in this article. These include aspects such as wood quality, cut resistance, resistance to moisture, odor neutrality and sustainability.
So, the choice of cutting board wood should be based on these specific wood characteristics. Let’s now take a closer look at some of these essential wood features, such as wood hardness, wood porosity, antibacterial and toxic properties of wood, which you should pay special attention to in your decision-making process.
The Hardness Level
The hardness of the wood plays a crucial role in choosing the right wood for a cutting board. It affects the resistance to knife cuts and wear, the lifespan of the wooden cutting board, and its ability to absorb food juices.
And, of course, the hardness of the wood affects the weight of the cutting board, which can make a significant difference in handling, especially with large and thick cutting boards. Boards made of harder wood are indeed more durable but also much more labor-intensive in terms of manufacturing and processing. What influences the hardness of the wood?
TYPE OF WOODS
These differences in tree species lead to varying cell structure and wood composition, which in turn affects the hardness level. Hardwoods have more fibers and narrower vessels, with a tighter and more uniform cell structure. Softwoods, on the other hand, have a less dense structure due to cavities filled with air, which makes them lighter than denser hardwoods.
The age of the wood
The reason for this relationship lies in the slow and steady compression and solidification of the wood’s core over the years. With the tree’s advancing age, more cell structures and mineral deposits form in the wood, resulting in increased density and hardness.
wood density
The harder the wood, the denser it is. Classification is done using the theoretical value of the anhydrous density, which determines the weight of the wood in complete dryness, a condition that never occurs in nature. Woods with an anhydrous density of less than 550 kg/m³ are softwoods, while hardwoods have an anhydrous density between 550 and 1,000 kg/m³. Ironwoods (some tropical woods) have an anhydrous density greater than 1,000 kg/m³ and are therefore too heavy to float on the water surface.
Growth conditions
Trees in the warm south enjoy longer growing seasons due to the mild climate. This results in the formation of more wood fibers and denser cell structures, making their wood harder and more resilient. Certain wood species in northern regions, where growing seasons are not as long, grow more slowly and become denser and harder. Fast-growing wood, often found near water sources, tends to be softer.
wood moisture
When wood absorbs moisture, the cell walls can swell, reducing the strength of the wood. Dry wood maintains its intact cell structure, leading to greater hardness.
wooden parts
Different parts of the tree can have varying levels of hardness. Heartwood and areas where branches have grown out from are harder than the outer regions of the trunk (bark).
Hardwood & Softwood Classification
As mentioned earlier, the classification of softwood and hardwood is done based on the so-called basic density. In this process, the wood is dried to 0% moisture content to enable comparable examinations without residual moisture. In this state, the density, which is the weight per unit volume (kg/m³), is determined.
Woods with a oven-dry density of more than 550 kg/m³ are classified as hardwoods, while those below are considered softwoods by definition.
This classification has nothing to do with whether the wood is evergreen or not, in other words, whether it is coniferous or deciduous. In English, the classification is based on botanical classification and does not indicate the actual wood hardness. In this context, “hardwoods” are referred to as tree species that shed their leaves in winter (deciduous trees), and “softwoods” are used for evergreen trees.
In most cases, this botanical classification is accurate. However, there are exceptions where softwoods are considered hardwoods and deciduous trees are classified as softwoods, especially when the classification is correctly based on oven – dry density, as illustrated in the following table.
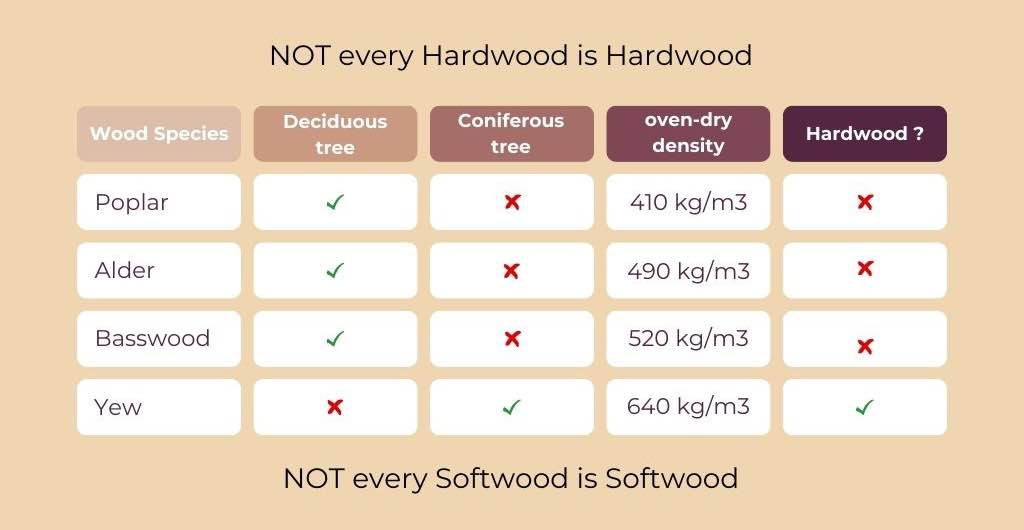
For our selection of woods for cutting boards, this classification is irrelevant, as we choose wood species with a density well above 550 kg/m³, making them hardwoods. The following hardness measurement method is more crucial for our wood selection.
Method for determining wood hardness
There are two common methods for measuring wood hardness: the Brinell method and the Janka method. Here are the main differences between these two methods:
Brinell Method:
The Brinell hardness measurement was developed in 1900 by the Swedish engineer Johan August Brinell and has since found widespread application in materials testing.
In this measurement, a 10 mm diameter tungsten carbide ball is used. This ball is pressed into the wood with a measured testing force. The exact testing force depends on the material’s density, as different materials have varying levels of resistance to penetration.
The wood must have a moisture content between 12% and 15% for this test.
The crucial aspect of the Brinell method is the dwell time: the ball is pressed into the test specimen for 15 seconds and then remains inside for an additional 30 seconds. This time period allows for sufficient deformation of the test material.
The results of the hardness measurement are expressed in the unit N/mm² (Newtons per square millimeter). This value represents the hardness of the wood, particularly its resistance to plastic deformation from penetration.
The Brinell hardness measurement is certified according to ISO standards, ensuring precise comparability of the results. Therefore, this hardness measurement is of great significance for quality control and material selection in various industrial sectors.
Janka Method:
The Janka hardness test is a widely used method in the United States, primarily employed by the hardwood flooring industry to compare the hardness of wood. This method was developed by the Austrian wood technologist Gabriel Janka (1864–1932).
The method for determining Janka hardness involves pressing a steel ball, approximately 12 mm (0.44 inches) in thickness, into the wood grain until it has penetrated about half of its diameter.
The applied force is subsequently measured in Newtons (N) or pounds of force (lbf). It is important to note that 1 Newton (1N) is approximately equal to 0.22481 pounds of force (lbf). This measured force forms the basis for calculating the Janka rating. The more force required to embed the ball, the higher the Janka rating, indicating greater wood hardness and resistance.
Let’s take maple wood as an example. In the Janka hardness test, a force of 6,000 Newtons (6,000N) is applied to the wood, which is approximately equivalent to 1,350 pounds of force (1,350 lbf). This specific value of 1,350 is listed in relevant wood hardness databases and serves as the Janka rating for maple wood.
To determine wood hardness using the Janka and Brinell methods, numerous databases are available on the internet.
German-language database (Janka & Brinell)
English-language database (Janka)
Right Hardness for Wood to use for Cutting Boards
As we already know, the right wood hardness is crucial to meet the requirements of a good cutting board. Wood that is too soft can leave deep cutting marks and is susceptible to increased liquid absorption, while wood that is too hard tends to dull knife blades faster and makes the cutting board heavy.
In the next section, we will take a look at the hardness levels of different wood species to give you an idea of which woods are suitable. As an extreme example, Australian Buloke is listed as one of the hardest woods, while Balsa is listed as one of the softest woods.
Suitable woods for cutting boards fall within a range of 900 to 1500 on the Janka hardness scale. Wood with a hardness rating in this range prevents knife blades from dulling quickly and meets other requirements for a high-quality cutting board. The optimal range for Brinell hardness is between 20 and 40.
Hardness Rating for common Cutting Board wood types
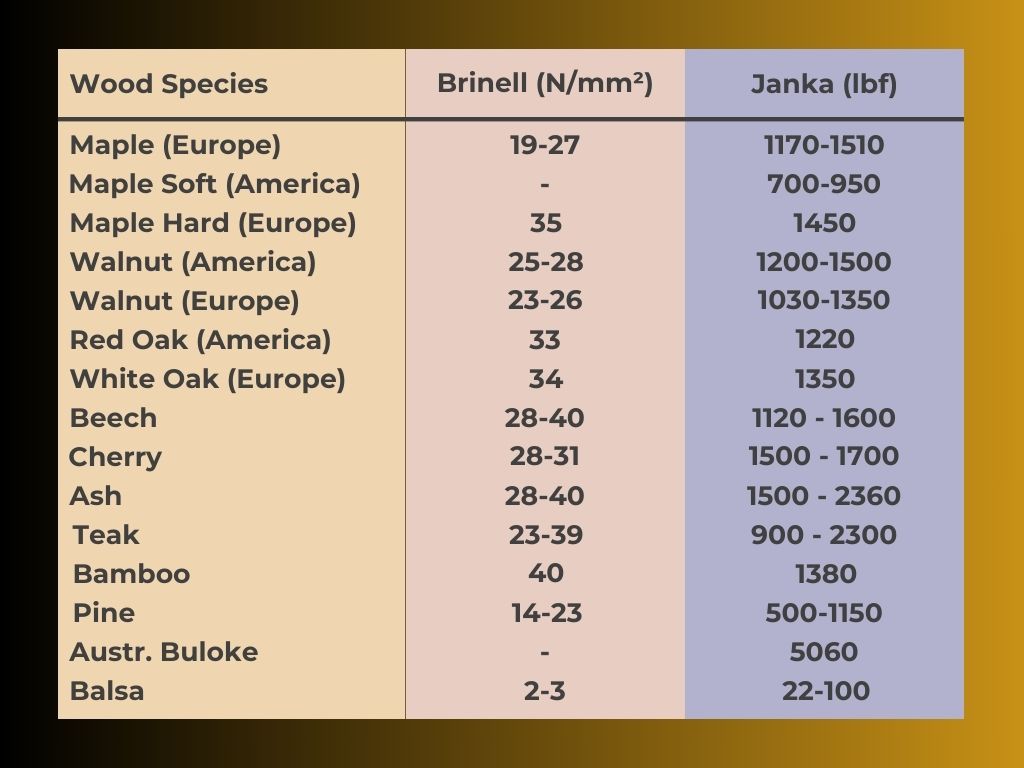
Porosity
Explaining Porosity
In materials science, porosity refers to the presence of pores – tiny empty spaces or voids that are distributed throughout the material.
Porous materials consist of a cohesive solid structure with interconnected pores that allow liquids and gases to permeate through them. In contrast, non-porous or impermeable materials lack such passage pores, making them impermeable to liquids and gases.
The porosity of a material affects almost all of its physical and chemical properties. Some aspects influenced by the porosity of a material include:
Permeability: Porous materials enable liquids to infiltrate and pass through them based on their pore size, distribution and interconnectivity.
Strength: Porous materials tend to be weaker due to their larger surface area, hollow pores and discontinuities.
Absorption: Materials with porous structures absorb more liquids depending on the extent of porosity.
Weight: Porous materials generally weigh less compared to non-porous materials of the same volume due to the presence of empty spaces.
Durability: Porous materials are more susceptible to damage from abrasion, chemicals and weathering since fluids can infiltrate pores.
All these aspects are taken into consideration when assessing the requirements for cutting boards and are factors to consider when choosing good wood for cutting board.
Porosity in Wood
Wood is composed of cells, with the two main types being vessel and fiber cells.
Vessel cells form elongated tubes along the grain to transport water and minerals in the tree.
The presence of fiber cells in wood is essential for providing a strong and stable support system. Although fiber cells are strong, they have micropores in their cell walls.
Wood’s porosity results from the presence of elongated pores within the vessel cells and, to a lesser extent, in the cell walls of fiber cells. These pores essentially form empty spaces, creating a complex network of pores in wood.
The type and arrangement of these cell types determine the level of porosity in different wood species.
Within hardwoods and softwoods, porosity also varies with density and the uniformity of their grain. Some woods like maple exhibit consistent porosity.
When using end-grain boards, it’s important to note that the grain and vessel cells are exposed. End-grain boards tend to absorb liquids to a greater extent. Therefore, it is essential to treat end-grain boards thoroughly with high-quality oils that penetrate deeply, and it’s necessary to reapply the wear layer in the form of wax at regular intervals. In particular, end-grain boards only function properly with a suitable finishing treatment.
Impacts of Wood Porosity
Strength and Longevity
Greater porosity means larger and more interconnected pores, weakening the wood’s structure. As a result, highly porous woods tend to be less stable and more susceptible to mechanical impacts, such as knife cuts
Moisture Absorption
Higher porosity allows for faster ingress and egress of moisture through the wood’s empty spaces. Porous woods respond more quickly to changes in moisture, resulting in swelling (expansion) or shrinking.
Weight
Wood is lighter than non-porous materials because it contains pores filled with lightweight air. However, wood density remains the primary factor influencing weight.
Surface Properties
Porosity influences surface characteristics like smoothness and the ability to absorb finishes evenly. Non-porous wood has smoother and shinier surfaces, while porous wood tends to have a matte appearance.
Maintenance Needs
Due to faster moisture absorption and release, porous wood requires more frequent protection from liquids and maintenance. Non-porous wood is less demanding and retains surface treatments (such as oils) longer.
Minimizing Wood Porosity
Sealing Techniques
Surface treatments like oiling and waxing with high-quality, food-safe products penetrate the top layer and fill the outer pores of the wood. They create a protective barrier that reduces moisture penetration but doesn’t completely inhibit it. The wood remains “breathable.” These applications should be repeated at regular intervals to ensure long-term protection.
Filling Solution
Hardening fillers like food-safe, multi-component epoxy resins are poured into knots or highly porous areas of the wood. They harden within the pores to create a non-porous surface. However, filling the pores can alter the appearance of the wood.
Porosity and Food Safety
The fact is that the wooden cutting board is an essential part of our kitchen for food preparation. This also means that food safety plays a crucial role in using cutting boards for a healthy home.
In this context, wood porosity plays a crucial role, as porous wood tends to absorb liquids more easily. Bacteria can penetrate and proliferate within the pores. Furthermore, working with knives on porous wood surfaces leaves cut marks and scratches that facilitate the ingress and growth of bacteria.
Some wood types, such as oak, have proven antimicrobial properties that can help reduce the risk of foodborne illnesses. However, it is important to note that they cannot completely prevent them.
Every wood naturally has pores that can absorb liquids. A high-quality wooden cutting board, therefore, requires the right type of wood with low porosity and appropriate surface treatment. This combination ensures a long lifespan for your cutting board.
Antimicrobial Properties
Studies have indicated that wood may possess natural antibacterial properties that help reduce harmful bacteria or prevent their growth. These properties can be attributed to two main factors:
Quelle: https://www.wilms.com/Hygiene/forschungen/BBA_HolzEinNW.pdf
Pine (phenolic compounds in pine heartwood) and oak (high content of phenols – tannic acids/tannins) are types of wood that can exhibit particularly positive antibacterial properties.
Another study, conducted by scientists from the University of Wisconsin, examined the antibacterial properties of wood, particularly in the context of its use as a cutting board. The study found that 99.9% of the bacteria placed on a wooden cutting board died within minutes. After being left at room temperature overnight, there were no living bacteria detectable on the wooden boards the next day. The study was published in the Journal of Food Protection in 1993.
A study conducted in 2019 and published in the Scirp journal found that different types of wood possess unique anatomical and chemical characteristics that can have specific effects on microbes. The research demonstrated that various wood metabolites influence the cell walls and membranes of microorganisms, and these effects vary depending on the type of wood. In simpler terms, this study looked at woods like larch, oak, pine, maple, cherry and beech, among others and found that they each have distinct properties that can interact with and affect microbes in different ways.
The Bavarian State Ministry of Food describes in an article a study conducted by the Anhalt University of Applied Sciences in Bernburg regarding the antibacterial properties of wood.
According to the current state of scientific knowledge, we can’t make a blanket statement about the antibacterial properties of wood. They need to be assessed on a case-by-case basis because they primarily depend on the type of wood itself, as well as other factors such as the type and concentration of bacteria, wood moisture, environmental temperatures, and relative humidity. Further standardized studies in this regard would still be necessary.
Toxicity of Wood
The safety of wood that comes into contact with food is of utmost importance for a good reason. Certain types of wood contain natural toxins that can leach into the food during cutting, potentially leading to poisoning or allergic reactions. However, there is a simple rule of thumb: woods that produce edible fruits, nuts, leaves, or sap are generally considered safe for food contact.
Wood to avoid in cutting boards
While exotic woods may be visually appealing, they should be avoided. These woods are not sustainable and often contain toxins that can leach from the wood and into the food placed on the cutting surface. Therefore, it is advisable to prioritize safety and food compatibility when selecting the good wood for cutting board.
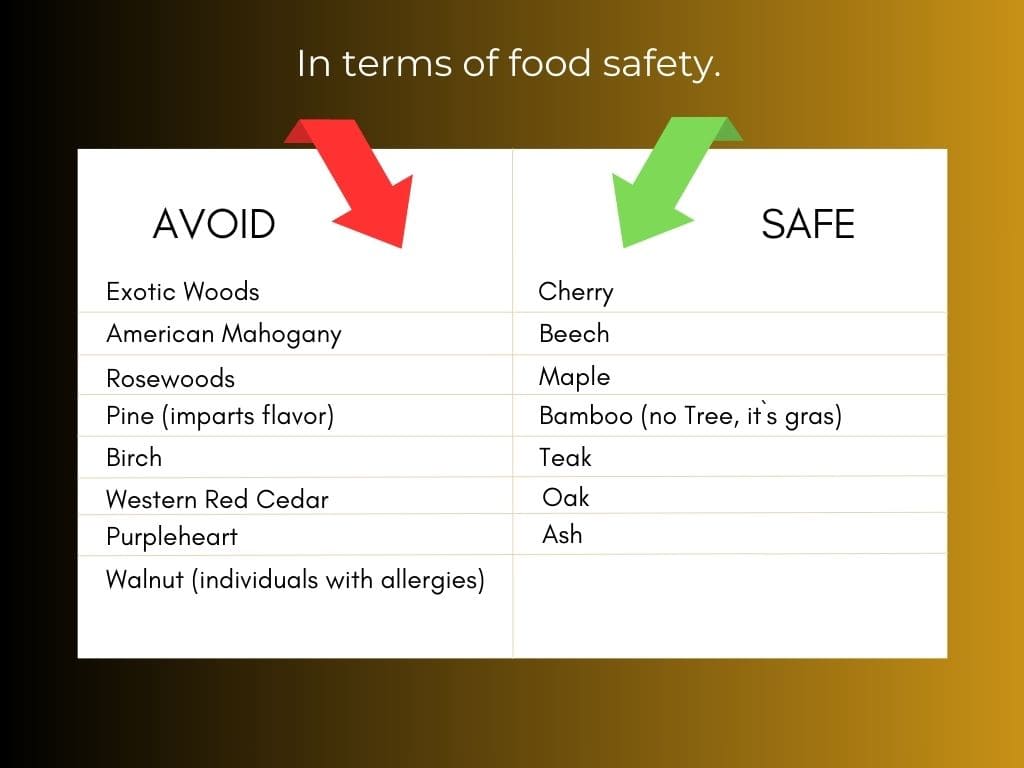
Please note that individuals may react differently to environmental influences. The list provided is intended as a guideline and is not exhaustive. As mentioned, it should be considered in every assessment that cutting boards always require surface treatment, which, if carried out carefully and with high-quality, food-safe products, provides additional, though not complete, protection against potentially harmful substances.
As for working with wood in terms of the release of dust through sanding or sawing, the health risk is entirely different. Personal protection against allergy-inducing, irritating, and toxic fine wood dust particles is a prerequisite for a healthier approach to working with wood. You will find information on this topic here shortly.
Costs of Wood
In general, as is the case everywhere else, the higher the wood quality, the more expensive it is.
Here are the key factors that determine the price of wooden products and the wood to use for cutting boards:
QUALITY OF WOOD
The quality of the wood plays a crucial role in pricing. High-quality wood, such as hardwood, is typically more expensive than lower-quality wood. Wood with a higher grade classification comes at a higher cost.
Supply and demand
When the demand for wood products is high and the supply is scarce, prices usually increase.
Procurement and Transport Costs
The costs for procuring and transporting wood can vary depending on the location of the wood supplier and the buyer. Higher transportation costs can result in higher prices.
degree of processing
The more a wood product has been processed by the retailer, the more expensive it typically is. Planed wood is more expensive than sawn wood of the same type. Pre-glued and often pre-sanded planed wood is even more cost-intensive. A solid wood panel with continuous lamellae is significantly more expensive than the often offered cheaper finger-jointed panels in hardware stores. Costs increase notably as the panels become thicker and longer, especially when they have continuous lamellae.
TYPE OF WOOD
Hardwoods like oak, beech, and ash are generally more expensive than softwoods like spruce or pine. Availability, of course, also plays a significant role. Exotic woods like cherry, apple, or plum, as well as walnut and other exotic woods, are even more costly.
Storage and Drying
Wood that has already been dried and seasoned is usually more expensive than fresh and moister wood that still needs to be dried. When purchasing wood, there is a distinction between AD (Air dried) and KD (kiln-dried).
Dimension
The thickness and length of solid wood planks and glued solid wood panels influence the price, with the price of solid wood planks also depending solely on the purchased quantity in cubic meters.
Economic and political factors
can also have an impact on wood prices. For example, rising energy costs or trade restrictions can lead to higher wood prices. In our experience, wood prices were up to 100% more expensive during the COVID-19 pandemic.
Sustainability
Wood from protected sustainable forestry is more expensive than mass-produced wood, which may be illegally harvested and environmentally damaging.
Assessing these factors leads to important conclusions. Essentially, only hardwood with a residual moisture content of <12% is the best material for cutting board, which already forms the basis for higher costs.
However, the pricing varies based on whether you acquire your material from a regional source or purchase it already planed and sanded.
To illustrate the extent of price differences, I’ve listed common and suitable wood types below. The prices are approximate values, given in €/m³, excluding VAT, and are from the year 2021.
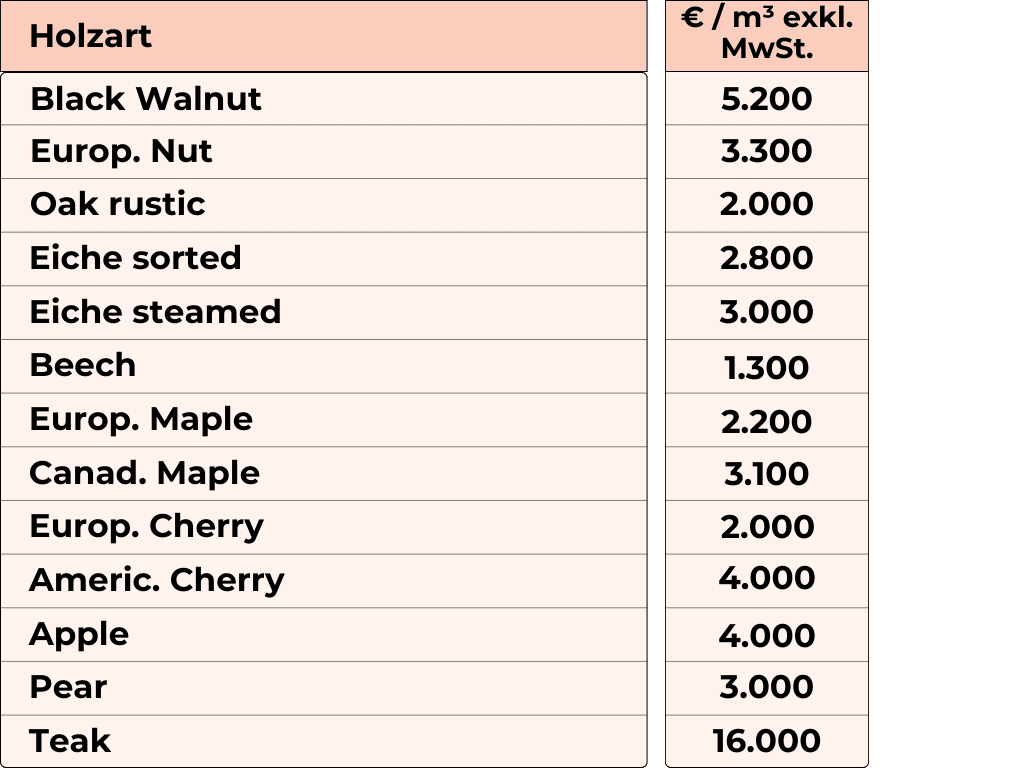
Best woods for a cutting board
The following overview presents a selection of wood to use for cutting boards.
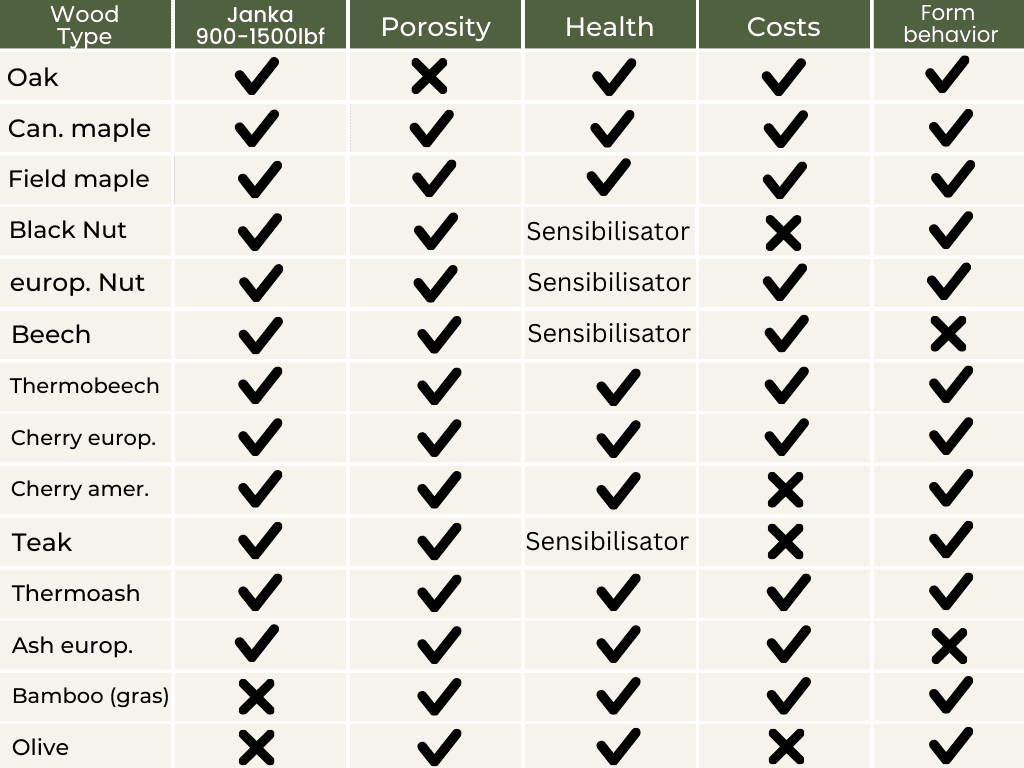
Pros and Cons of specific wood types
Teak
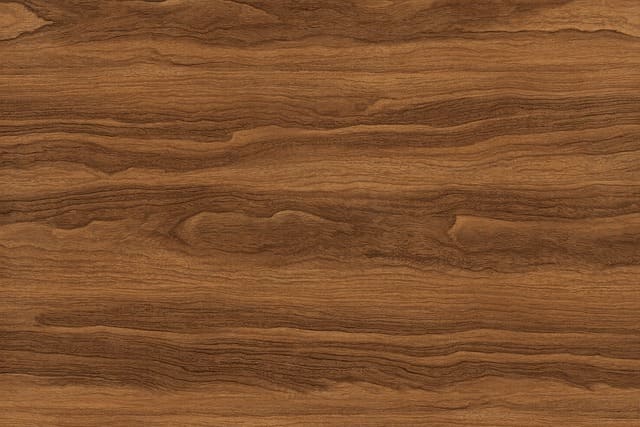
PRO
- Distinctive in appearance with a pronounced grain
- Moisture-resistant and dimensionally stable
- Fine grain, dense structure
CONTRA
- expensive
- partially subject to import sanctions
- distinctive odor (rubber-like)
- oily surface
- abrasive to knives (due to SiO2 inclusions)
- can be very hard
OAK
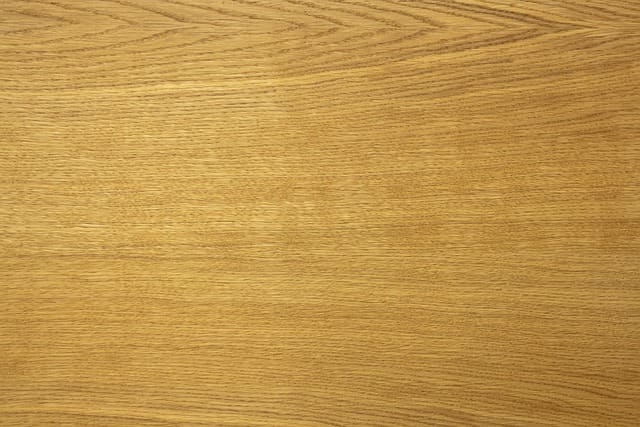
PRO
- accentuated after surface treatment
- highly durable as an end-grain board
- good price-to-performance ratio, readily available
- easy to work with
CONTRA
- More porous than comparable hardwoods
- Suitable for long boards with limitations
- May react with metal (tannic acid)
- Demanding on knives due to a rough surface texture
- Variable in hardness depending on the type of oak
EUROP. MAPLE
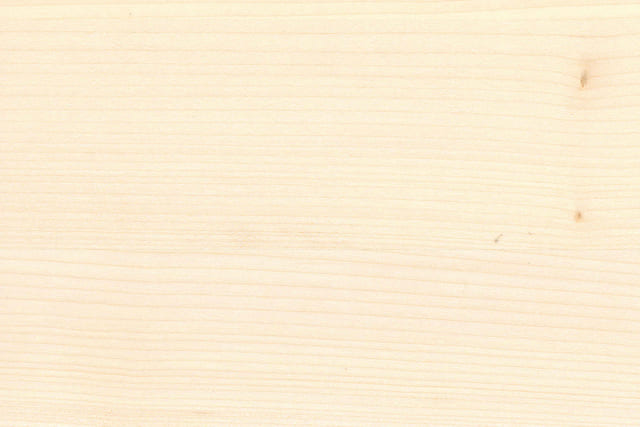
PRO
- uniform very light surface appearance
- partially pearl-like appearance
- fine-pored and dense structure
- good price ratio, good availability
- easy to work with sharp tools
- as an end-grain board, it’s very sturdy with beautiful grain – best material for cutting board
CONTRA
- Long-grain boards are somewhat more prone to cutting damage and may not be as moisture-resistant.
AMERICan WALNUT
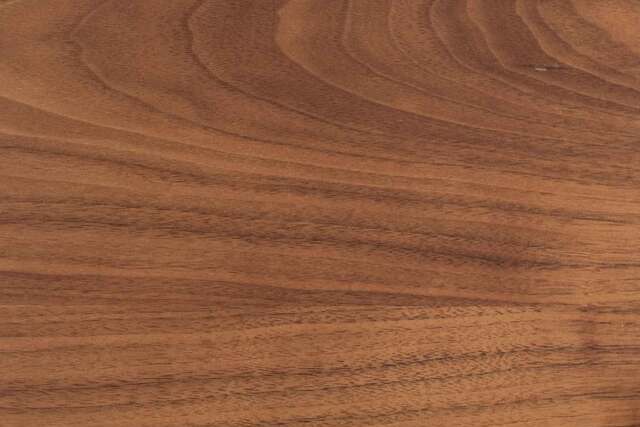
PRO
- unique dark and contrasting surface appearance
- fine-grained and dense structure
- readily available
- easy to work with
- as an end-grain board, it is exceptionally sturdy with a beautiful grain pattern
CONTRA
- expensive
- can be allergenic.
- variable hardness, hence limited for use as a long-grain board.
EUROPean WALNUT
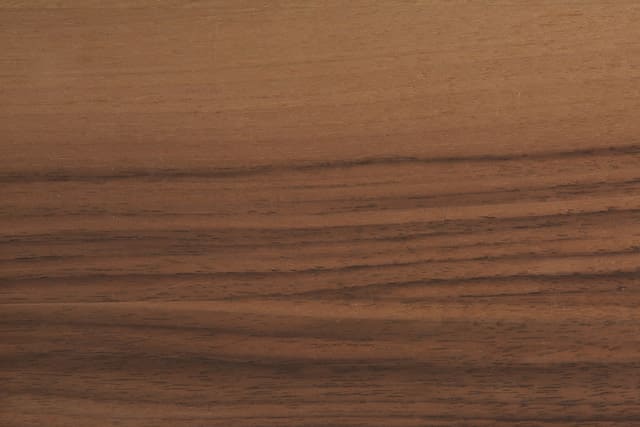
PRO
- Light to dark appearance (not as dark as American walnut)
- Fine-grained and dense structure
- Very easy to work with sharp tools
- As end-grain boards, it’s exceptionally strong with a beautiful grain pattern
CONTRA
- Price-intensive (precious wood)
- can be allergenic
- can be very hard
EUROPean CHERRY
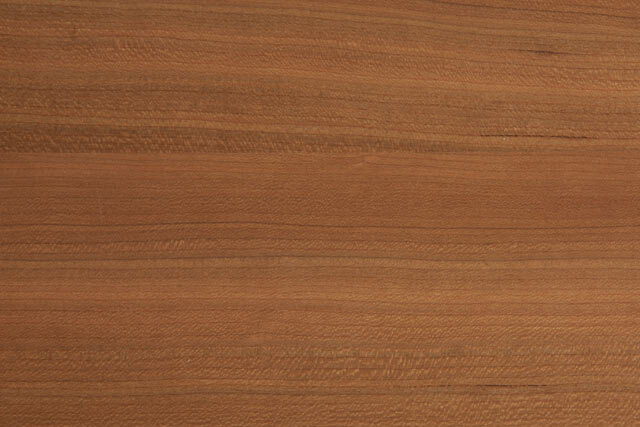
PRO
- Light to dark red appearance (American cherry is darker)
- Fine-pored and dense structure
- Very easy to work with sharp tools
- As an end-grain board, it’s solid with a fantastic grain pattern
- Excellent for adding accents
CONTRA
- Price-intensive
- Limited in longboard variation, suitable for accents (narrow strips)
- Noticeable differences in hardness, especially near the sapwood area
- Limited availability
BAMBOO (GRAS)
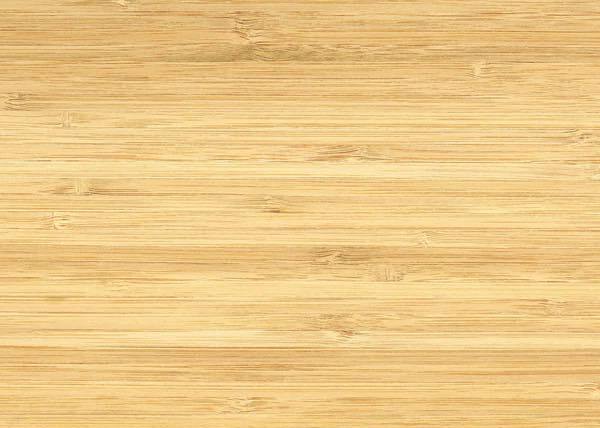
PRO
- Inexpensive
- Lightweight
- Fast-growing
- Bright appearance
CONTRA
- Very hard
- SiO2 deposits dull knives
- Long transportation routes to Europe
- Young bamboo works intensively
BEECH

PRO
- Inexpensive alternative
- Not overly dull for knives
- Possesses a good level of hardness
- Readily available
- Distinctive appearance
CONTRA
- Prone to staining.
- Less dimensionally stable as an end-grain board.
My Choice
In my narrowed selection of good wood for cutting board, you will find oak, European and American walnut, European maple and European cherry. These cutting board wood types have proven themselves without reservation for the production of end-grain cutting boards.
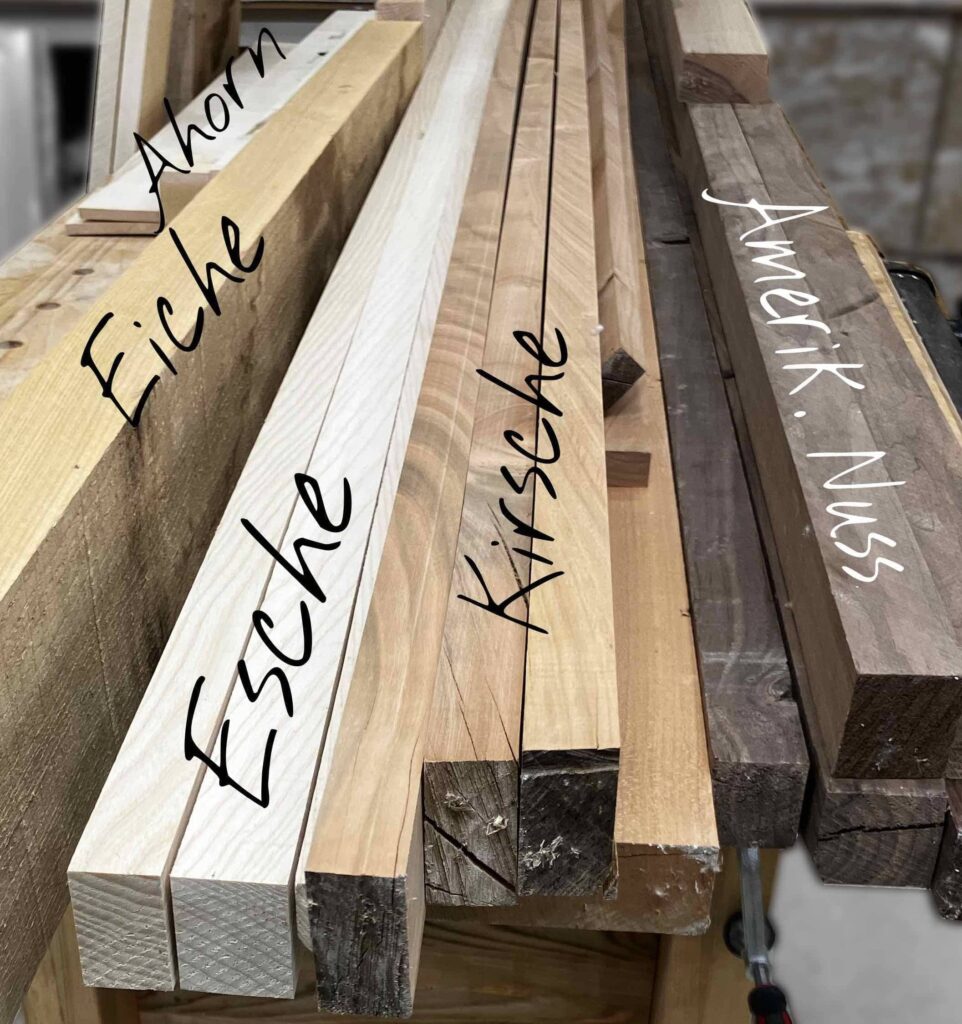
An exception arises with oak when used as a long grain board, especially when frequent cutting is involved. Its coarse fibers can become susceptible to sharp knives when exposed to moisture. However, oak is perfectly suitable for less demanding purposes, such as a casual snack board or a solid BBQ board.
Conclusion
Choosing the good wood for cutting board is of paramount importance and is dependent on several critical factors.
Wood hardness and porosity play a central role in determining the board’s longevity. Additionally, wood types may offer positive attributes such as appealing surface texture and antibacterial properties. The potential toxicity of the wood should also be carefully considered.
Naturally, the costs of acquiring high-quality and suitable wood for cutting boards are a significant factor.
It is vital to emphasize that optimal surface treatment is crucial for the long-term functionality of a good cutting board.
While there are approximately 25,000 different wood species worldwide, I can confidently say from personal experience that oak, walnut, cherry, maple and ash are reliable and proven choices. These cutting board wood types have proven themselves in practice.
Hopefully, this article can aid you in your decision-making process, whether you are crafting and constructing your own cutting board or contemplating a new purchase.